System Function Introduction
Beautiful interface, simple operation, electronic industry terms are easy to understand and use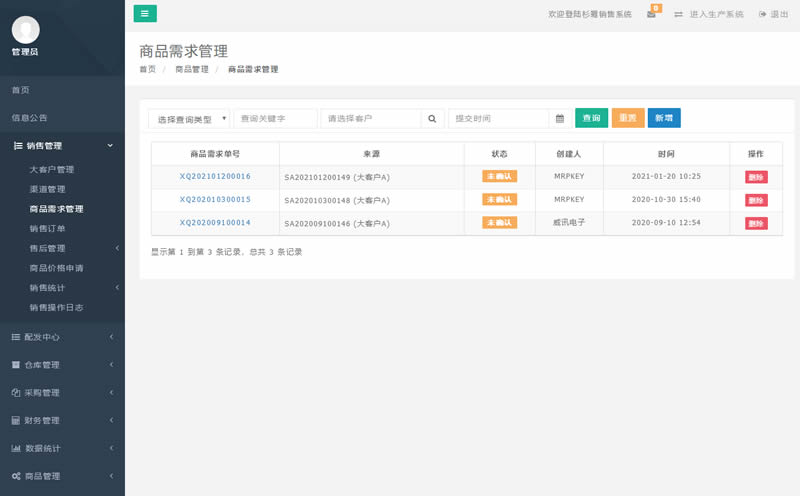
Sales Management
Manage demand orders and convert customer demand plans into production demand orders. Sales personnel can view the real-time completion of production work orders related to orders, so as to reduce the waste of resources caused by ineffective communication;
Managing trade commodities enables you to understand the inventory data of self-produced products or trade commodities in real time. It not only includes the basic purchase, sales and inventory management, but also extends the sales statistics report, and flexibly customizes the sales strategy through various report data.
Production Management
It is divided into production work orders (in normal production status) and scheduled work orders (i.e. planned work orders);
After the production work order is approved, the materials required by the work order are locked immediately. For the re created production work order, the available quantity after deducting the occupation (lock quantity of the previous work order) has been displayed for the same material inventory;
The production demand document converted from the sales order is then created as a scheduled work order, and the production mode (self owned processing or subcontract production) and production quantity are confirmed by referring to the current existing product inventory.
Set production scheduling and planned completion date, confirm the shortage of planned work orders, and reasonably arrange procurement or production line production.
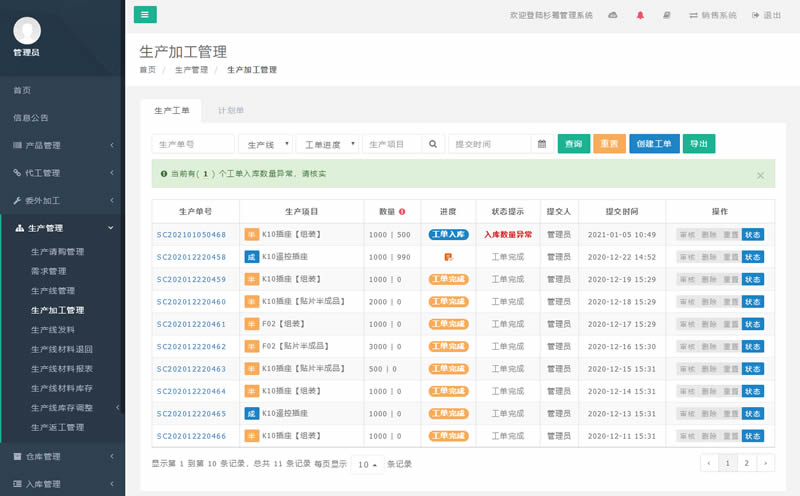
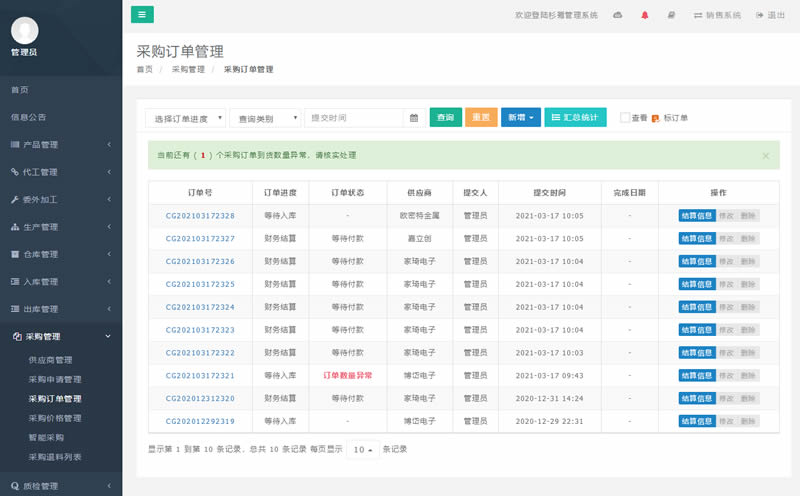
Purchasing Management
There are two material purchase modes: general purchase and intelligent purchase;
For general purchase, you can purchase by supplier or by material. Select the supplier and the supplied material item, and enter the purchased material quantity. The operation is simple and fast;
The powerful intelligent purchase function can select to import production items, production work orders or demand scheduling to generate the corresponding required material gap quantity. At the same time, it can also help you calculate the minimum order quantity and unit packaging quantity of materials, and generate purchase orders of multiple suppliers after confirmation.
Warehouse management
Including receipt management and issue management, you can view the warehouse inventory, the actual quantity of material warehouse, the quantity waiting for receipt (i.e. the quantity in transit of purchase) and the production consumption in real time;
It also includes functions such as material transfer between warehouses and material inventory adjustment (error correction);
According to the material inventory or packaging quantity, work order issue and distribution can be flexibly selected. Insufficient materials can be partially issued first, and then distributed again after the purchase is qualified and received.
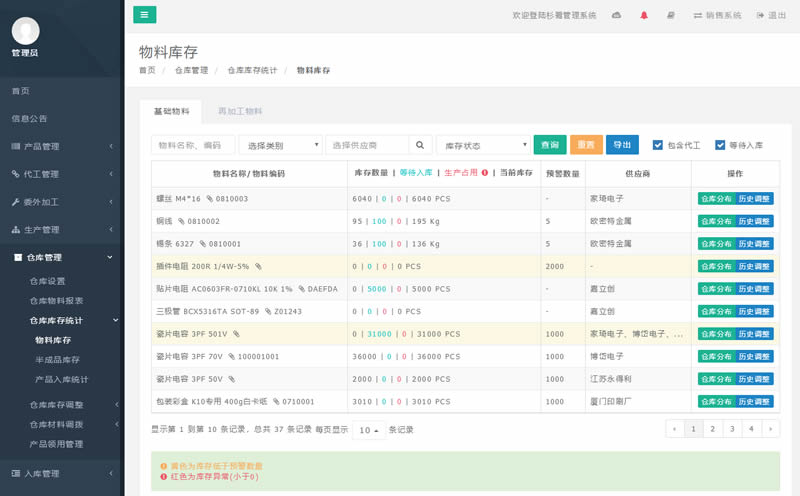
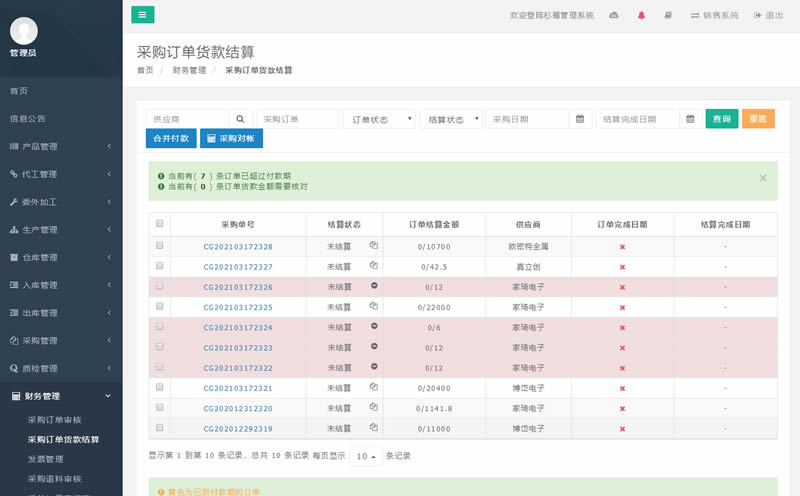
Financial Management
Including purchase payment settlement, invoice management, subcontracting expenses, sales order payment settlement, sales reconciliation, etc;
Purchase payment settlement can remind the due payable payment according to the supplier's accounting period, or perform reconciliation settlement through the purchase receipt document;
Subcontracting expense settlement can calculate the processing expense of actually delivered products according to the subcontracting expense settings of products, or perform reconciliation settlement according to the subcontracting product receipt document.
BOM Management
Product BOM management is divided into semi-finished product management and finished product management. Multiple BOM tables (bill of materials) can be set for production differentiation management;
The creation of BOM is simple and fast. It supports import and batch setting. It can also set the usage base, PCB tag number and production loss rate for each material;
BOM can retain multiple historical versions to facilitate traceability;
At the same time, you can also view the real-time material cost price of each finished product and semi-finished product BOM to better control the product cost and reduce the enterprise capital risk.
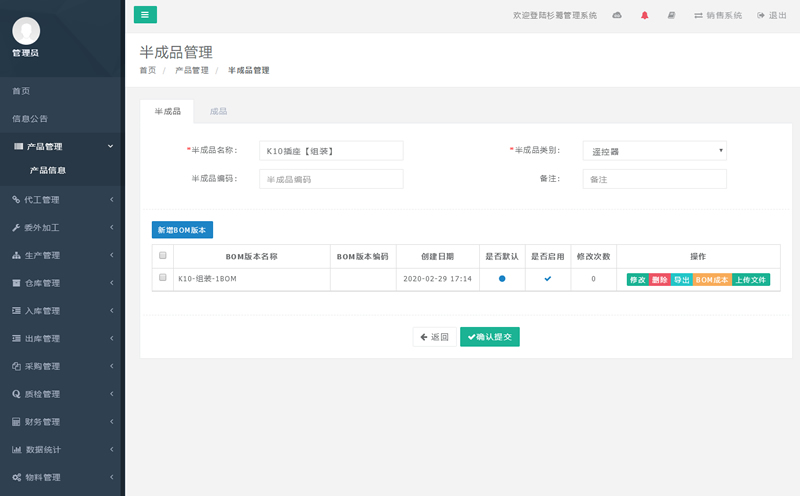
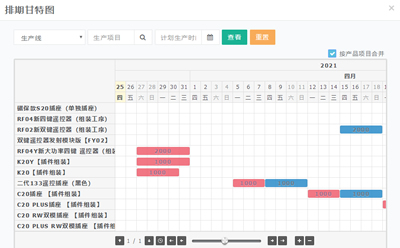
Statistic Chart
Rich statistical charts: Gantt chart of production scheduling, statistics of product production in the same period (chain relative ratio), and etc;
The chart has various and intuitive forms, and can master the production data in real time to help you make decisions or revise the production plan quickly.
For more solutions to business scenarios, scan our wechat QR code of the technical consultant for remote online demonstration.